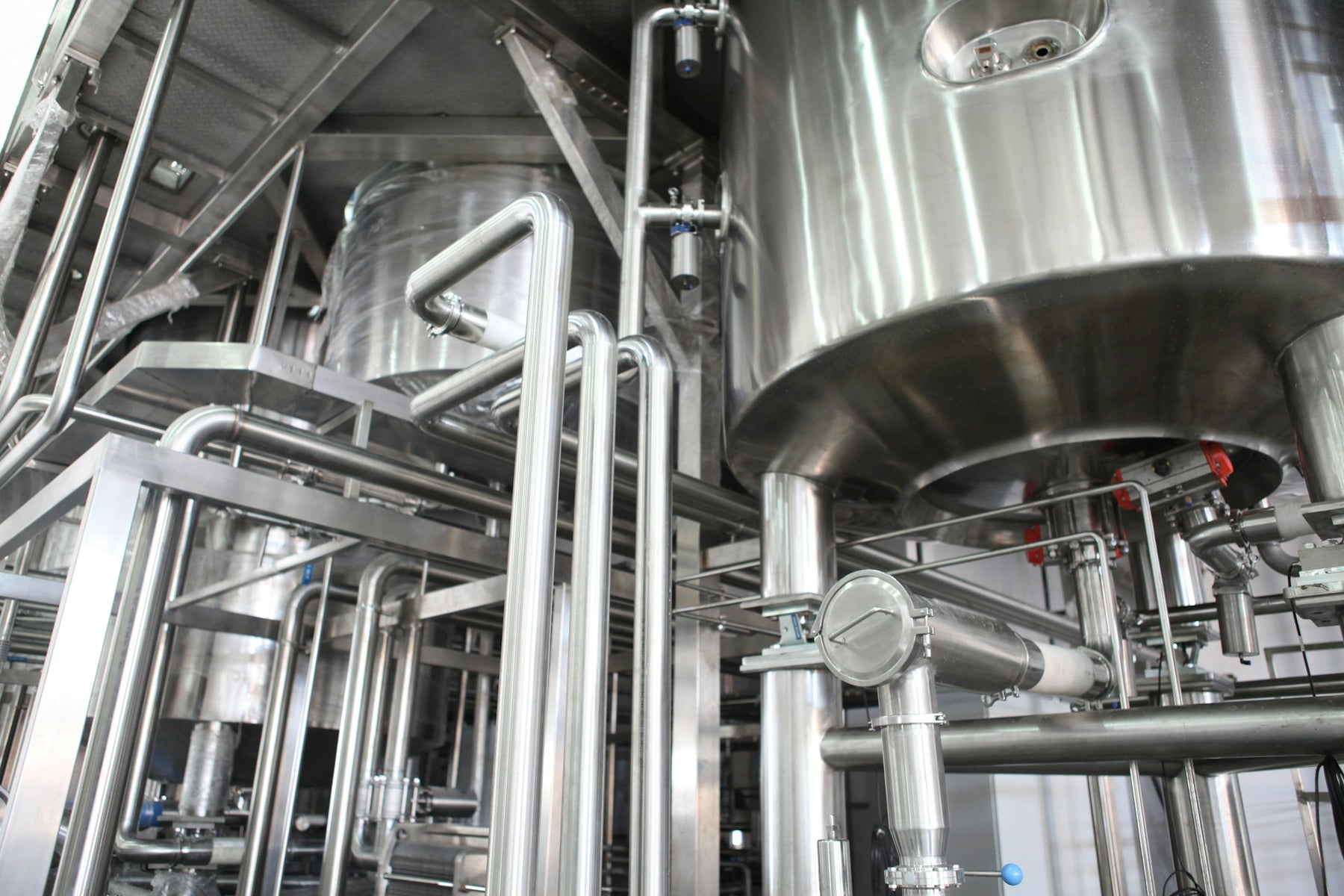
Why choose fluoropolymers over PVC, rubber, and other materials?
In the realm of industrial applications, the selection of tubing materials is a critical decision that directly impacts operational efficiency, safety, and cost-effectiveness. Among the myriad options available, fluoropolymer tubing stands out for its exceptional chemical resistance, temperature tolerance, and inertness. In this blog post, we'll explore three industrial use cases and compare the benefits of fluoropolymer tubing to alternative materials, highlighting its superior performance and versatility.
Chemical Processing
In chemical processing plants, where corrosive chemicals and aggressive solvents are prevalent, tubing materials must withstand harsh environments without compromising performance or integrity. Fluoropolymer tubing, such as PTFE and PFA, offers unparalleled chemical resistance, making it an ideal choice for conveying corrosive fluids and reactive chemicals.
Example: In a chemical manufacturing facility, fluoropolymer tubing is used to transport concentrated sulfuric acid for pH adjustment in various chemical processes. Traditional materials like PVC or rubber would quickly degrade under the acidic conditions, leading to leaks, contamination, and safety hazards. Fluoropolymer tubing ensures reliable and long-lasting chemical transport, minimizing downtime and maintenance costs.
Semiconductor Manufacturing
The semiconductor industry demands precision and cleanliness in manufacturing processes to ensure the quality and reliability of electronic components. Tubing used in semiconductor fabrication must exhibit ultra-high purity, low particle generation, and compatibility with harsh chemicals and high temperatures. Fluoropolymer tubing meets these stringent requirements, offering exceptional purity, minimal extractables, and resistance to aggressive etchants and solvents.
Example: In semiconductor cleanrooms, fluoropolymer tubing is employed in critical processes such as chemical vapor deposition (CVD) and wafer cleaning. Unlike stainless steel or polyethylene tubing, which may introduce contamination or particle generation, fluoropolymer tubing maintains ultra-pure conditions, safeguarding the integrity of semiconductor devices and optimizing yield.
Food and Beverage Production
In the food and beverage industry, tubing materials must comply with stringent regulatory standards for food safety while withstanding harsh cleaning chemicals and temperature fluctuations. Fluoropolymer tubing, with its inertness, non-stick properties, and resistance to cleaning agents, offers an ideal solution for conveying liquids and gases in food processing and bottling plants.
Example: In a beverage bottling facility, fluoropolymer tubing is used to transfer carbonated beverages from mixing tanks to filling machines. Traditional materials like PVC or silicone may absorb flavors or harbor bacteria, compromising product quality and safety. Fluoropolymer tubing ensures hygienic and contamination-free transport, preserving the freshness and integrity of beverages.
Comparative Analysis
1. Chemical Resistance: Fluoropolymer tubing offers superior resistance to a wide range of corrosive chemicals, outperforming materials like PVC, rubber, or stainless steel, which may degrade or corrode over time.
2. Purity and Cleanliness: In industries requiring ultra-high purity and cleanliness, such as semiconductor manufacturing, fluoropolymer tubing excels in minimizing particle generation and maintaining product integrity compared to alternative materials.
3. Temperature Tolerance: Fluoropolymer tubing withstands extreme temperatures, making it suitable for applications in chemical processing and industrial environments where other materials may fail or degrade.
Fluoropolymer tubing emerges as a superior choice for a diverse range of industrial applications, offering unmatched chemical resistance, purity, and reliability. By selecting fluoropolymer tubing over traditional materials, industries can enhance operational efficiency, ensure product quality and safety, and minimize maintenance costs and downtime, ultimately driving sustainable growth and innovation.
Chemical Processing
In chemical processing plants, where corrosive chemicals and aggressive solvents are prevalent, tubing materials must withstand harsh environments without compromising performance or integrity. Fluoropolymer tubing, such as PTFE and PFA, offers unparalleled chemical resistance, making it an ideal choice for conveying corrosive fluids and reactive chemicals.
Example: In a chemical manufacturing facility, fluoropolymer tubing is used to transport concentrated sulfuric acid for pH adjustment in various chemical processes. Traditional materials like PVC or rubber would quickly degrade under the acidic conditions, leading to leaks, contamination, and safety hazards. Fluoropolymer tubing ensures reliable and long-lasting chemical transport, minimizing downtime and maintenance costs.
Semiconductor Manufacturing
The semiconductor industry demands precision and cleanliness in manufacturing processes to ensure the quality and reliability of electronic components. Tubing used in semiconductor fabrication must exhibit ultra-high purity, low particle generation, and compatibility with harsh chemicals and high temperatures. Fluoropolymer tubing meets these stringent requirements, offering exceptional purity, minimal extractables, and resistance to aggressive etchants and solvents.
Example: In semiconductor cleanrooms, fluoropolymer tubing is employed in critical processes such as chemical vapor deposition (CVD) and wafer cleaning. Unlike stainless steel or polyethylene tubing, which may introduce contamination or particle generation, fluoropolymer tubing maintains ultra-pure conditions, safeguarding the integrity of semiconductor devices and optimizing yield.
Food and Beverage Production
In the food and beverage industry, tubing materials must comply with stringent regulatory standards for food safety while withstanding harsh cleaning chemicals and temperature fluctuations. Fluoropolymer tubing, with its inertness, non-stick properties, and resistance to cleaning agents, offers an ideal solution for conveying liquids and gases in food processing and bottling plants.
Example: In a beverage bottling facility, fluoropolymer tubing is used to transfer carbonated beverages from mixing tanks to filling machines. Traditional materials like PVC or silicone may absorb flavors or harbor bacteria, compromising product quality and safety. Fluoropolymer tubing ensures hygienic and contamination-free transport, preserving the freshness and integrity of beverages.
Comparative Analysis
1. Chemical Resistance: Fluoropolymer tubing offers superior resistance to a wide range of corrosive chemicals, outperforming materials like PVC, rubber, or stainless steel, which may degrade or corrode over time.
2. Purity and Cleanliness: In industries requiring ultra-high purity and cleanliness, such as semiconductor manufacturing, fluoropolymer tubing excels in minimizing particle generation and maintaining product integrity compared to alternative materials.
3. Temperature Tolerance: Fluoropolymer tubing withstands extreme temperatures, making it suitable for applications in chemical processing and industrial environments where other materials may fail or degrade.
Fluoropolymer tubing emerges as a superior choice for a diverse range of industrial applications, offering unmatched chemical resistance, purity, and reliability. By selecting fluoropolymer tubing over traditional materials, industries can enhance operational efficiency, ensure product quality and safety, and minimize maintenance costs and downtime, ultimately driving sustainable growth and innovation.