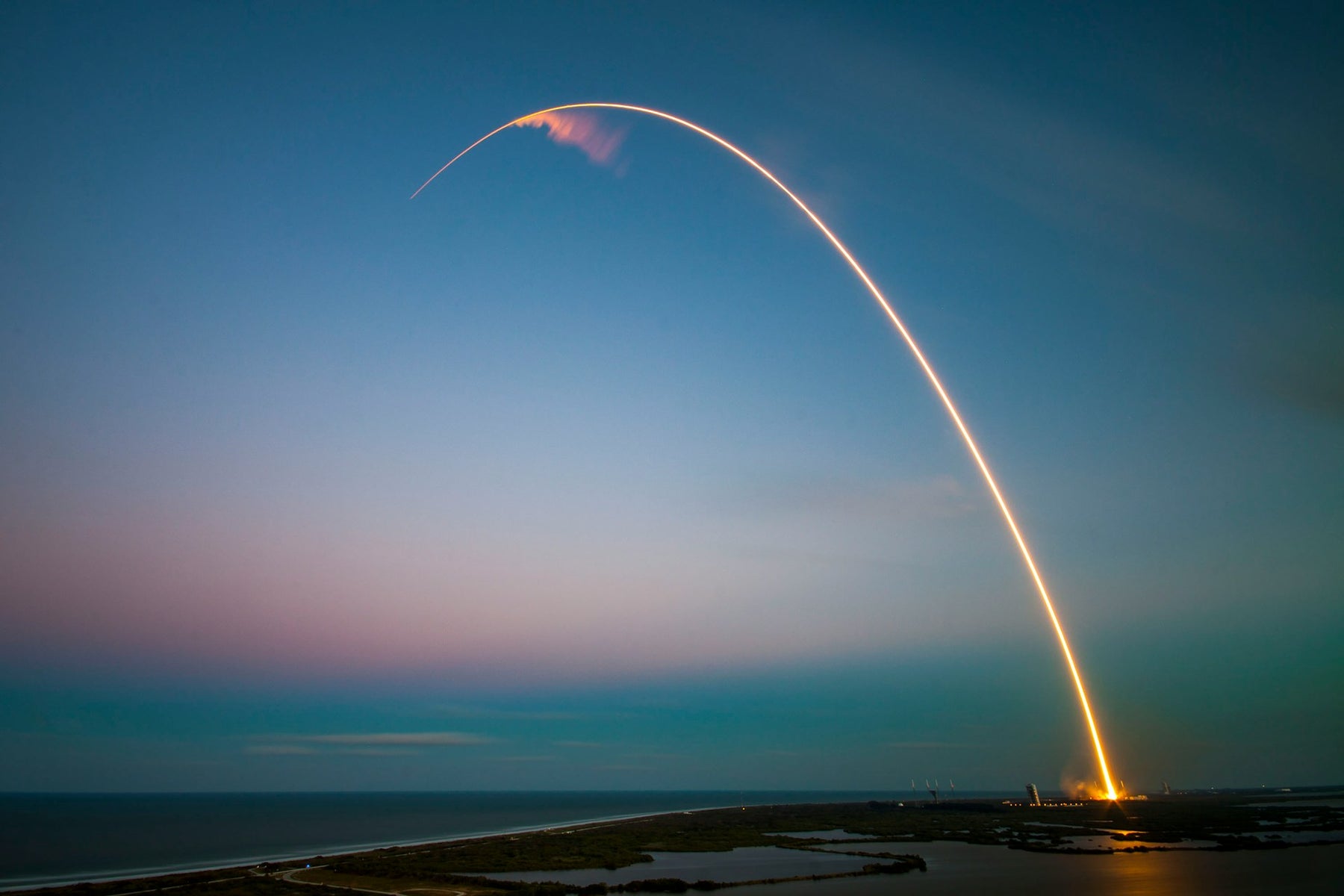
Fluoropolymers launch another one to the stars!
The journey of Boeing’s Starliner spacecraft to the stars represents a significant milestone in space exploration. It is a testament to human ingenuity and technological advancement. Amidst the myriad components and sophisticated engineering that made this mission possible, fluoropolymers play an indispensable role. Known for their exceptional chemical resistance, thermal stability, and mechanical strength, fluoropolymers are crucial in various aerospace applications.
Ensuring Structural Integrity and Thermal Management
High-Temperature Resistance: Spacecraft components must endure extreme temperatures, from the frigid vacuum of space to the scorching heat during re-entry. Fluoropolymers such as PTFE (Polytetrafluoroethylene) and PFA (Perfluoroalkoxy) are renowned for their thermal stability. They maintain their structural integrity and performance across a broad temperature range. These materials are used in various seals, gaskets, and insulation components, ensuring they could withstand the intense heat of launch and re-entry without degradation.
Lightweight Strength: One of the paramount concerns in spacecraft design is weight. Every additional kilogram requires more fuel and increases costs. Fluoropolymers provide a unique combination of lightweight properties and exceptional mechanical strength. Components such as hoses, tubing, and various structural elements made from fluoropolymers contribute to reducing the overall weight of the Starliner while maintaining the necessary durability and resilience.
Enhancing Safety and Reliability
Chemical Resistance: The Starliner’s fuel and propulsion systems rely on handling highly reactive and corrosive chemicals. Fluoropolymers, including FEP (Fluorinated Ethylene Propylene) and ETFE (Ethylene Tetrafluoroethylene), offer superior resistance to a wide range of chemicals. These materials are used in fuel lines, seals, and protective coatings, ensuring that the spacecraft's critical systems remained intact and functional, even when exposed to aggressive substances.
Electrical Insulation: Reliable electrical systems are vital for the operation of any spacecraft. Fluoropolymers are excellent electrical insulators, providing protection against electrical arcing and ensuring stable signal transmission. PTFE and other fluoropolymers are used to insulate wiring and electronic components, safeguarding the spacecraft’s avionics and communication systems from electrical failures.
Improving Efficiency and Performance
Low Friction Properties: The movement and control mechanisms within the Starliner required materials that could operate smoothly and efficiently. Fluoropolymers, particularly PTFE, have a very low coefficient of friction. This property is invaluable in components such as bearings, seals, and sliding surfaces. The use of fluoropolymer components ensure that mechanical systems operated with minimal friction, reducing wear and tear and enhancing the longevity and reliability of the spacecraft.
Hydrophobicity: The hydrophobic nature of fluoropolymers helps in preventing the accumulation of ice or moisture on critical components. In the harsh environment of space, where condensation and ice formation can pose significant risks, the hydrophobic properties of materials like PTFE and FEP ensure that sensitive equipment remains dry and operational.
Supporting Human Spaceflight
Life Support Systems: In crewed missions, ensuring the safety and comfort of astronauts is paramount. Fluoropolymers play a critical role in the life support systems. They were used in air and water filtration systems, ensuring that the air and water supplied to astronauts were free from contaminants.
Cabin Insulation and Protection: The interior of the crew module also benefits from fluoropolymer materials. They provided thermal insulation, protecting astronauts from the extreme temperatures outside the spacecraft. Additionally, fluoropolymers are used in fire-retardant materials to enhance the safety of the crew cabin.
Future Implications and Innovations
Sustainable Space Travel: The use of fluoropolymers is a step towards more sustainable and reliable space travel. Their durability and resistance to harsh conditions mean that components made from these materials have longer lifespans and require less frequent replacement, reducing waste and resource consumption.
Advanced Materials Research: The success of fluoropolymers in these missions encourages further research into advanced materials for space applications. Innovations in fluoropolymer technology could lead to the development of new materials with even greater performance characteristics, driving advancements in space exploration.
Ensuring Structural Integrity and Thermal Management
High-Temperature Resistance: Spacecraft components must endure extreme temperatures, from the frigid vacuum of space to the scorching heat during re-entry. Fluoropolymers such as PTFE (Polytetrafluoroethylene) and PFA (Perfluoroalkoxy) are renowned for their thermal stability. They maintain their structural integrity and performance across a broad temperature range. These materials are used in various seals, gaskets, and insulation components, ensuring they could withstand the intense heat of launch and re-entry without degradation.
Lightweight Strength: One of the paramount concerns in spacecraft design is weight. Every additional kilogram requires more fuel and increases costs. Fluoropolymers provide a unique combination of lightweight properties and exceptional mechanical strength. Components such as hoses, tubing, and various structural elements made from fluoropolymers contribute to reducing the overall weight of the Starliner while maintaining the necessary durability and resilience.
Enhancing Safety and Reliability
Chemical Resistance: The Starliner’s fuel and propulsion systems rely on handling highly reactive and corrosive chemicals. Fluoropolymers, including FEP (Fluorinated Ethylene Propylene) and ETFE (Ethylene Tetrafluoroethylene), offer superior resistance to a wide range of chemicals. These materials are used in fuel lines, seals, and protective coatings, ensuring that the spacecraft's critical systems remained intact and functional, even when exposed to aggressive substances.
Electrical Insulation: Reliable electrical systems are vital for the operation of any spacecraft. Fluoropolymers are excellent electrical insulators, providing protection against electrical arcing and ensuring stable signal transmission. PTFE and other fluoropolymers are used to insulate wiring and electronic components, safeguarding the spacecraft’s avionics and communication systems from electrical failures.
Improving Efficiency and Performance
Low Friction Properties: The movement and control mechanisms within the Starliner required materials that could operate smoothly and efficiently. Fluoropolymers, particularly PTFE, have a very low coefficient of friction. This property is invaluable in components such as bearings, seals, and sliding surfaces. The use of fluoropolymer components ensure that mechanical systems operated with minimal friction, reducing wear and tear and enhancing the longevity and reliability of the spacecraft.
Hydrophobicity: The hydrophobic nature of fluoropolymers helps in preventing the accumulation of ice or moisture on critical components. In the harsh environment of space, where condensation and ice formation can pose significant risks, the hydrophobic properties of materials like PTFE and FEP ensure that sensitive equipment remains dry and operational.
Supporting Human Spaceflight
Life Support Systems: In crewed missions, ensuring the safety and comfort of astronauts is paramount. Fluoropolymers play a critical role in the life support systems. They were used in air and water filtration systems, ensuring that the air and water supplied to astronauts were free from contaminants.
Cabin Insulation and Protection: The interior of the crew module also benefits from fluoropolymer materials. They provided thermal insulation, protecting astronauts from the extreme temperatures outside the spacecraft. Additionally, fluoropolymers are used in fire-retardant materials to enhance the safety of the crew cabin.
Future Implications and Innovations
Sustainable Space Travel: The use of fluoropolymers is a step towards more sustainable and reliable space travel. Their durability and resistance to harsh conditions mean that components made from these materials have longer lifespans and require less frequent replacement, reducing waste and resource consumption.
Advanced Materials Research: The success of fluoropolymers in these missions encourages further research into advanced materials for space applications. Innovations in fluoropolymer technology could lead to the development of new materials with even greater performance characteristics, driving advancements in space exploration.