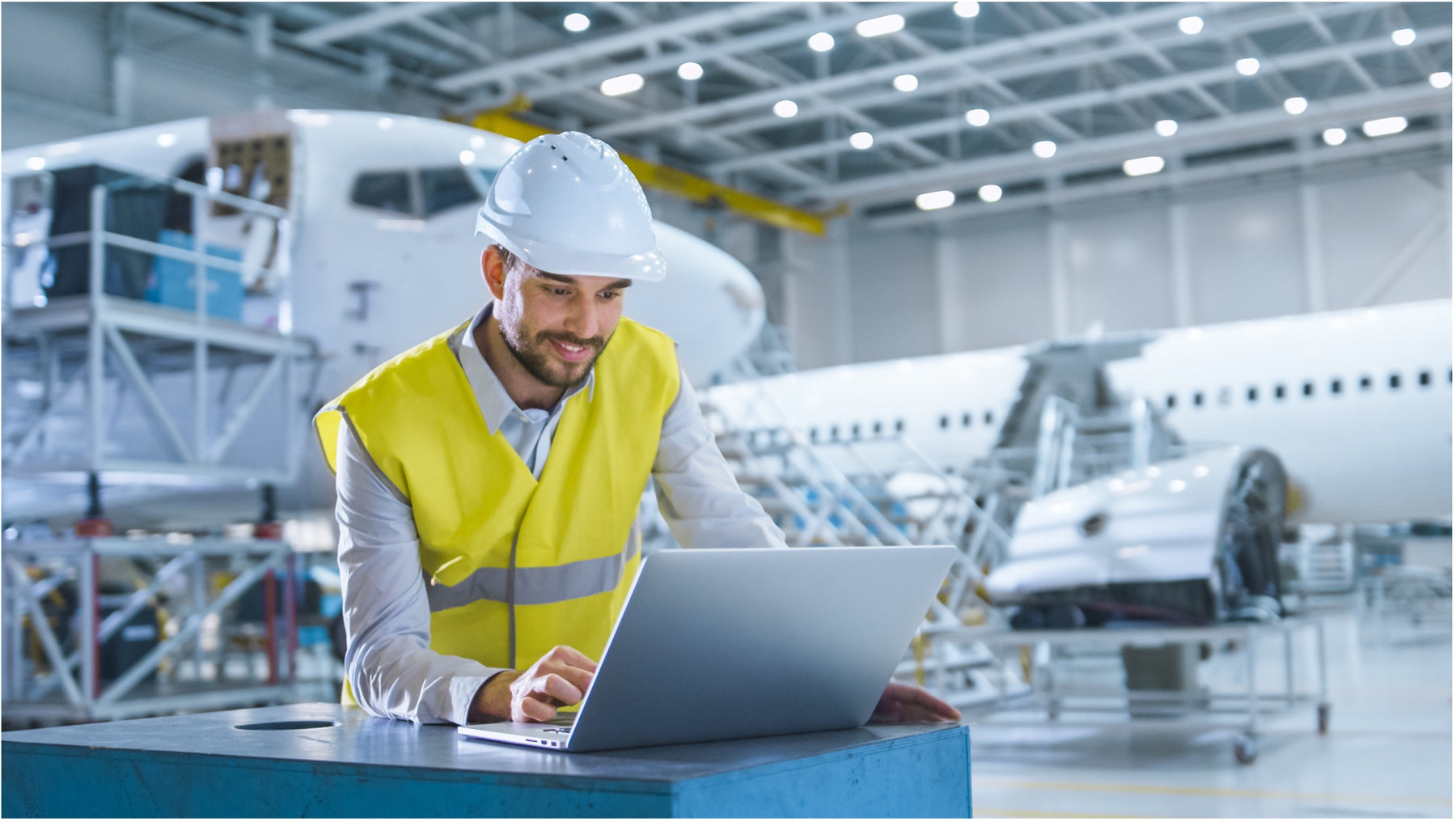
The importance of fluoropolymers in airplane parts to make flying possible
Have you ever wondered what goes into aeronautical engineering? Flight has been one of humankind’s most significant accomplishments and today is one of the most used forms of travel, with an average of 4 billion passengers a year. While commercial flight has become one of the most common forms of transportation, the public’s understanding of flight remains relatively limited. While on average it takes up to 5 years to understand every element of an aircraft and become a professional aeronautical engineer, readers can gain a basic understanding of a few essential airplane parts by reading below.
Winglets
Have you ever looked out an airplane window and wondered why the wings of the aircraft lift at the end? Firstly, these structures are called winglets and hold great significance for flight. Winglets were first invented during the early days of aviation; however, NASA researchers were credited with discovering the importance of winglets for flight stability. Dr. Richard Whitcomb, an aerospace engineer at NASA Langley Research Center, first tested winglets and compare them to longer wings in a wind tunnel. During his study, Dr. Whitcomb discovered that the winglet would improve aircrafts cruising efficiency by 6-9%, with futures tests revealing that winglets also increased an aircraft’s mileage by 6.5%.
Empennage
An empennage, also known as the tail section of an aircraft, consists of a tail cone, stabilizers, and remote-controlled aerodynamic surfaces. The tail cone of the Empennage is used to streamline the aft end of the fuselage (main compartment of the aircraft), while the cone is made up of structural members. Essentially, the Empennage is used to stabilize the aircraft during flight and provides a surface for the stabilizers to be mounted. During the flight, the Empennage's stabilizers allow the plane to fly in a straight line and reduce gusts of wind blowing the aircraft from side to side.
Fluoropolymers
Finally, any material that goes into airplane engineering must be able to withstand extreme temperatures, erosive chemicals, battering winds, and other extreme variables. While aircrafts were originally built using wood, cloth, lightweight metals, today’s commercial aircraft industry requires aircrafts to be able to withstand the elements at great heights and carry weight up to 175,000 lbs. For this reason, the aerospace industry has come to rely heavily on fluoropolymers due to their resilience against the elements, abrasion, and harsh chemicals. Furthermore, fluoropolymer’s lightweight composition allows for greater aircraft speed, agility, and less frequent refueling.