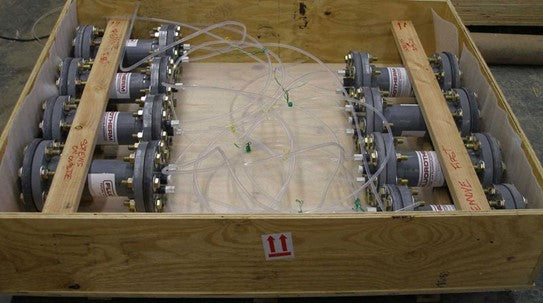
Maintenance and Cleaning Strategies for Shell and Tube Heat Exchangers
Shell and tube heat exchangers are designed for the in-line heating and cooling needs of industrial and commercial settings. Regardless of how well-made they are, these integral components are susceptible to fouling and corrosion, so proper maintenance and cleaning protocols are necessary in order to ensure consistent performance and longevity.
Those looking to service shell and tube heat exchangers should fully understand how to perform standard maintenance and cleaning, deal with corrosion, and handle fouling.
Regular Maintenance and Cleaning Steps
Used to transfer heat between fluids without mixing them, these exchangers are perhaps the most common type used in a range of settings. Knowing the correct procedural maintenance/cleaning steps is vital to their continued optimal performance.
- Inspect the exterior for signs of damage (e.g., cracks, leaks, wear, and tear) or corrosion, ensuring the exchanger is secured properly at the same time.
- Inspect the tube bundle for signs of corrosion or fouling. The latter occurs when solids build up on the tube’s surface, reducing efficiency.
- Check the fluids flowing through the exchange to confirm correct pressure and temperature. Check for signs of contamination or leaks as well.
- Clean the tubing following the methods below if corrosion or fouling is present. If only standard (i.e., light) fouling is present, chemical cleaning will suffice.
- Reassemble the exchanger, ensuring all components are reconnected and secured properly.
- Test for leaks, temperature, and pressure, ensuring the necessary adjustments are made for optimal performance.
While they may seem obvious, following the steps above (and maintaining vigilance for common issues) are integral to maintaining the long lifespan of these essential components.
How to Handle Corrosion
Generally speaking, corrosion happens when the material of the tube negatively reacts with the environment or fluids, causing leaks, reduced heat transfer, and thinning of the tube wall.
Prevention is the best course of action. Using corrosion-resistant materials (e.g., titanium or stainless steel) and applying protective coatings are common practice to prevent such happenings. However, testing and visual inspections still must be carried out to ensure early corrosion detection.
If extensive corrosion has already occurred, the components will need replacing. Hence, prevention measures should be followed at all times.
How to Address Tube Fouling
Tube fouling is the most common problem associated with shell and tube heat exchangers. It occurs when material (i.e., biological matter, scale, or dirt) accumulates on the inside or outside of the tube, reducing heat transfer, reducing system performance, and increasing the pressure drop.
You can address tube fouling in one of two ways, depending on its severity.
For light fouling, chemical cleaning will be sufficient. This method simply uses chemicals to dissolve and flush out the fouled material. For heavy fouling, however, mechanical cleaning is best. This involves removing the fouling material physically using a brush or water jet.
How to Address Mechanical Damage
Cracks or leaks are deemed as mechanical damage. Typically, such issues are addressed through tube replacements or repairs.
More often than not, servicers fix it by tube plugging — inserting a plug into the cracked section to prevent fluid leaks.